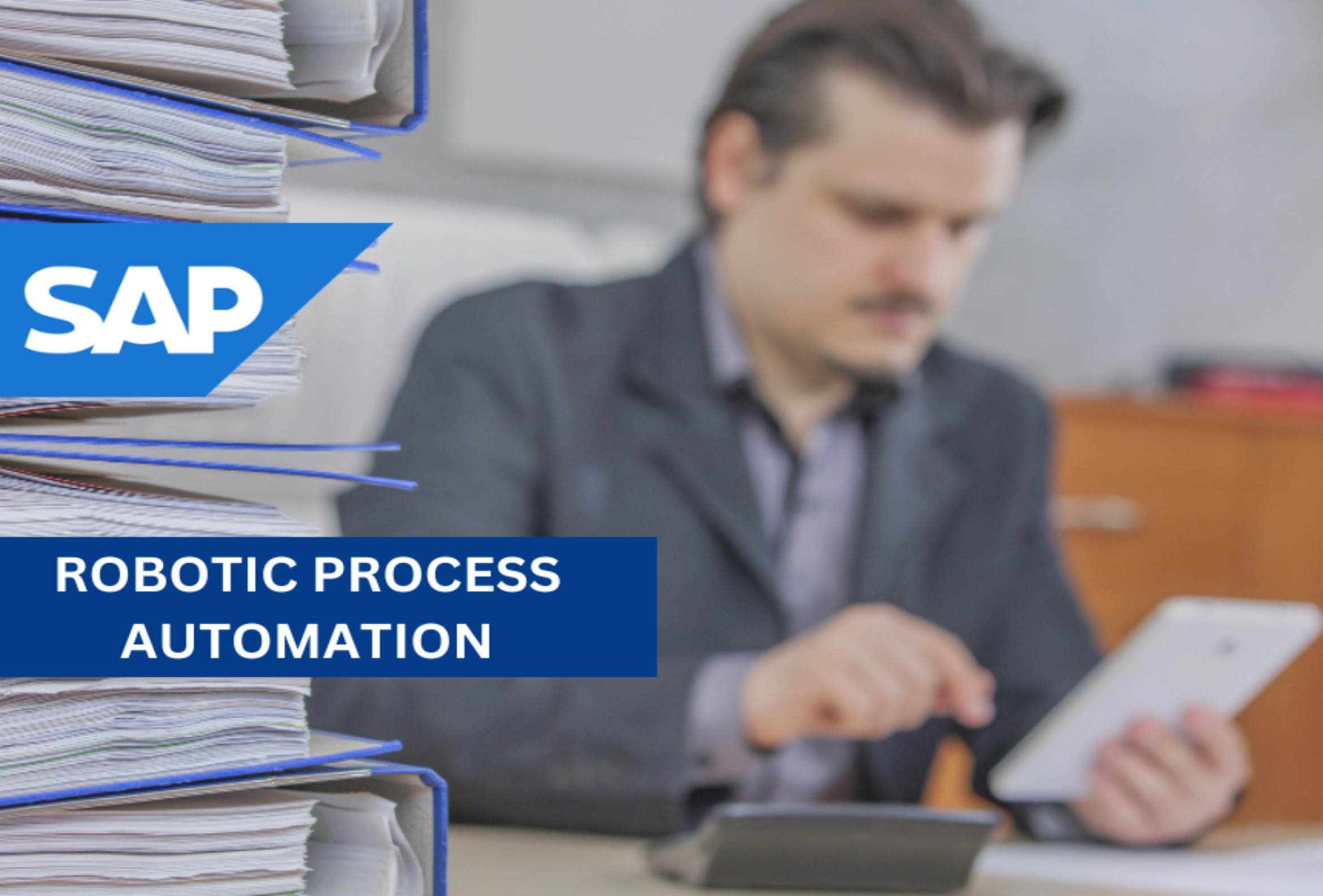
Key takeways
- Material Ledger is a complex tool that helps manage core manufacturing-related materials in different currencies and valuations.
- The original SAP R/2 and SAP R/3 software helped establish the global standard for Enterprise Resource Planning (ERP).
- Currently, SAP S/4HANA is being used to streamline several workflows in ERP. It supports technologies such as AI and ML.
- SAP S/4HANA also enables storing inventory values in multiple currencies. It also enhances scalability by optimizing the locking mechanism when material documents are created.
- Automating the Material Ledger Closing Process helps save manpower, cost, and time and increases accuracy.
Material Ledger is a complex tool offered by SAP. This tool helps manage core manufacturing-related materials in different currencies and valuations. It contains transactional data whose master data is contained in the material master. Material Ledger evaluates the prices of these items with the help of the stored data.
Before we dive into the automation of material ledger closing, let us briefly look at the complexities of material ledger closing.
The purpose of a material ledger is to generate financial transactions at a material level. It provides granular details of inventory management.
In a manufacturing setup, the product cost flow includes:
- Standard Cost Estimates
- Work in Progress/Variance/Settlement Processes according to different manufacturing processes.
- Material valuation through different stages of movement throughout the supply chain.
Material Ledger includes the above costs and also includes costing in multiple currencies.
Actual cost calculation is an important part of the Material Ledger process. includes the following steps:
- Production/process closing
- Overhead cost calculation
- Execution of assessment or indirect activity allocation cycles
- Actual cost split
- Actual activity price calculation
- Actual costing run in Material Ledger
A typical Material Ledger Closing Process goes through the following steps:
- Selection of all materials for the provided plants.
- Determining the sequence of costing starts with the lowest-level material and goes on to the highest-level material and assets.
- Calculating the prices of each item in the inventory.
- Calculating the price of the complete production stream.
- Adjustment posting of actual costs at the month-end based on where the actual consumption occurred.
- The next step is the post-closing step wherein all calculations performed in the previous steps are posted throughout this step.
All these calculations and a plethora of variables to be considered make material ledger closing a complex and time-consuming process.
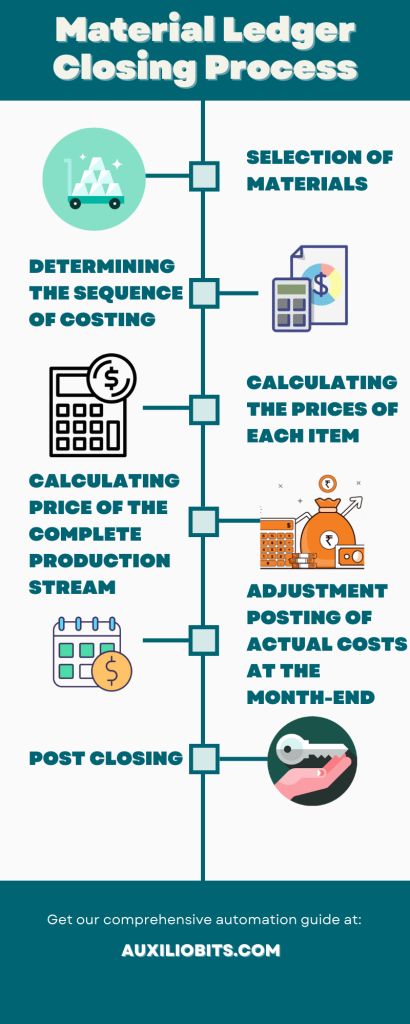
The SAP Intervention:
What is SAP?
The introduction of SAP, however, helped streamline multiple processes on a single platform. The original SAP R/2 and SAP R/3 software helped establish the global standard for Enterprise Resource Planning (ERP). With the introduction of intelligent automation, the capabilities of the original SAP software increased multifold. Currently, SAP S/4HANA is being used to streamline several workflows in ERP.
SAP S/4HANA can process large volumes of data with the power of in-memory computing. It can support technologies such as Artificial Intelligence (AI) and Machine Learning (ML). SAP S/4HANA replaces the process-driven legacy platforms and integrates all parts of business applications in a single intelligent suite on a digital platform
SAP process automation made a foray in 2018 when SAP workflow automation was used with intelligent Robotic Process Automation in a single package to automate workflows. The software uses a no-code or low-code drag-and-drop interface that is easy for business professionals and developers to automate workflows.
SAP in Material Ledger Closing Process:
Material Ledger is a mandatory element of inventory evaluation in the SAP S/4HANA. Material valuation is stored in the material ledger tables which facilitates dynamic Material Ledger reporting. Material Ledger also supports ad-hoc reporting. In SAP S/4HANA inventory valuation is available in a central repository or Universal Journal. However, the actual costing feature is optional.
While Material Ledger is an integral part of SAP, the specific use of Material Ledger can be customized according to your specific needs.
The costing process identifies the standard price and the real procurement price of goods in the product cost flow. These prices are recorded in the Material Ledger according to the movement of material. All the pricing data gathered is used for calculating Periodic Unit Price (PUP). PUP is further used to estimate the ending inventories and consumption.
SAP S/4HANA also enables storing inventory values in multiple currencies. It also eliminates redundant data. Besides, it enhances scalability by optimizing the locking mechanism when material documents are created.
Case Study:
Material Ledger Closing Process:-
There are several companies and each company has more than one plant. The staff needs to ensure that the previous and current status are clear before closing the material ledger.
How is this process done manually by a human?
In the manual process:
Every Thursday the price determination is done and closing entries are made. The price determination and closing entry are rechecked. In addition, the locked entries, and previous and current status of the plant are verified.
On Fridays, price determination and closing entries are checked. The current and previous statuses are verified and locked.
Every Sunday, the current status is checked. If the current status is not successful, it is corrected through a tedious and time-consuming process.
Every Monday checks are performed on the locks.
Each step is performed manually by the staff. The manual process is slow, complicated and prone to errors. Overall the process took 5 days to complete the entire cycle.
Automation Solution:
To Close the plant for the current period by UI path Robot.
On Thursdays and Fridays, bots are used to complete processes like price determination and closing entry. They perform various checks and verify the current and previous status.
On Sundays, the bots first check the current status. If the current status is incorrect, bots send emails to clients and create a new service request instead of executing the predefined query. Bots then check the status of the new query and if the query is resolved successfully, they verify the post-execution and current status. If the various entries are correct, the query is closed, otherwise, a mail is sent to the client to create a new service request.
On Mondays, bots check the lock.
The Difference:
Before automation, the person performed the same sequence of steps and updated the current and previous status of the plant, price determination, and closing entry, and also checked the lock on specific days mentioned in the description. Before automation Person was taking 5 days to perform this task manually. Now after automation, all the tasks take place in a few hours.
By automating the Material Ledger Closing Process we have saved Manpower, Cost, and Time and increased accuracy.
In this specific case, the automation solution was implemented in the SAP portal.
Material Ledger Closing automation tools must work precisely to reap the benefits of automation. The choice of the tool will depend largely on the specific needs of the organization. Hence, it is a good idea to take the help of an expert for choosing the software.
Auxiliobits has a team of experienced software professionals who help clients in choosing the best software for their processes. Our experts have years of experience in working with the manufacturing industry. We have an in-depth knowledge of how the different processes work. We recommend cost-effective automation software that is customized according to your specific needs.
Want to know more about how automation is disrupting the manufacturing ecosystem?
Watch this space for our future articles on automation!